第二回 射出成形課「業務改善への情熱」
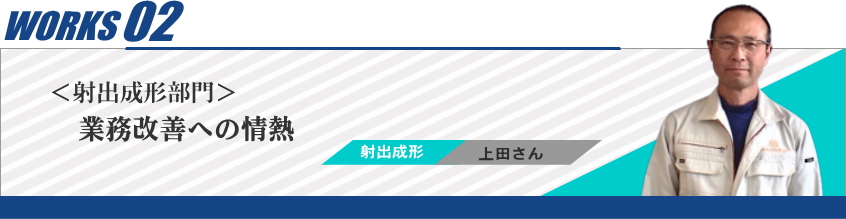
「現場に聴く! 職人インタビュー」では、ホームページだけではお伝えしきれないトウゴクセラミックの製造や生産管理などの情報を、現場へのインタビューを通して皆様にお伝えします。
第二回は、射出成形課の上田さんにお話を伺いました。
当社の射出成形課では、ジルコニア(ZrO₂)、アルミナ、炭化珪素(SiC)などの材質を、プレス成形や鋳込み成形では行えない三次元的な複雑形状の製品として生産しています。
今回はそんな射出成形課だけに留まらず、部署の垣根を超えたお客様の満足度向上を目指した、管理・改善業務に情熱を燃やす、「現場の声」をお届けします。
プラスチックのノウハウを元にセラミック射出成形(CIM)の分野へ
――本日はよろしくお願いします。まず、あなたの年齢、役職についてお答えください。
よろしくお願いします。上田です。56歳。射出成形も担当していますが、他の業務にも関わっているので、現状では役職という言い方をする事は難しいですね。
実はトウゴクセラミックでは、はっきりと名前の付いた役職を持っている方はそれほど多くはありません。
新しい試みを行っていく上で、既存の役職では足りない部分も出てきていると感じています。
社長とお話をさせてもらう機会も多いのですが、社長が代替わりした事もあり、組織が刷新される事もあるかと思います。今後は組織として、仕事をやる上での機能、役割、権限であったり、それが明確になった役職が決まっていくと思います。
――この仕事を始めて何年になりますか?
今年の4月で丸4年という形になります。
――以前はどのようなお仕事を?
元々は樹脂関係の仕事をしていました。
セラミックの業界とは全く違う職種でしたが、ものづくりの仕事だという事は共通しています。
現在の射出成形にもプラスチックの製品で関わっていました。
セラミックの成形に関わるのは初めてでしたが、使っている機械や、金型というツールなど、樹脂の射出成形と基本的には同じものなので、原料がセラミックに変わった事で違いをどう調整していくのか、特性をどう活かすのか、またそれを理解していくには、などと、既にあるノウハウと照らし合わせながら、今の製造を行っています。
――このホームページを見ている方の中には、「射出成形」と言っても馴染みのない方も居るかと思います。射出成形とはどういうものか、簡単に説明してもらえますか?
射出成形自体は、主にプラスチックの分野で使われる技法です。
例えば、プラモデルを作っている技法と言えば、ご理解いただけるかと思います
一般的には、普段目にするプラスチックの多くは射出成形で作られていると思います。
セラミックの成形には様々な技法があるのですが、トウゴクセラミックでも主力としているのはプレス成形です。
プレス成形は、アルミナなどの粉体をプレス、つまり圧力をかけて固める手法で、金属にも使われています。
一方、射出成形は樹脂などの原料を加熱し、溶かしたものを良品になるような条件で金型の中に流し込み、冷やして固めた後に、型から取り出す。簡単に言えば大判焼きのような作り方ですね。
これを機械的にエンドレスに作り続けられるようなものが射出成形機です。
これをセラミックの原料で行う事がCIM(セラミック・インジェクション・モールディング)という事になります。
射出成形だけではない様々な改善業務
――上田さんは射出成形以外にも多くの仕事に関わっていると伺ったのですが、その仕事を説明していただけますか?
まずは生産管理ですね。
元々、私は検査・出荷業務担当の想定で入社をしたのですが、品質的に問題が発生した場合、検査前に不良品が来ていたのでは出荷が出来ない、という事態も発生し得るわけです。
そこで「頭から、品質を作り込む」という改善を社長や工場長に提案した所、その方向性で進めていきたいと指示をいただきました。
そこから製品の歩留まり改善や、製品の不具合トラブルシューティングに関わるようになり、特定アイテムに限定して計画立案から出荷までを管理するようになりました。
検査前で製品を待っていても、悪いものが流れてきてしまえば出荷出来ないし、効率が悪いですからね。
このように部署を横断的に管理する事によって、少しずつですが今までよりも効率的に生産するサイクルになりつつあります。
本来、当社の検査・出荷部署は製品が出来たものだけを検査して出荷するという役割なのですが、
特定アイテムについては、受注したものをいつまでにどれほど出荷するのか、生産計画から出荷までをプランニングし、スケジューリングから不具合のトラブルシューティングまで、全て私が担当するスタイルで実践しています。
――受注が入った時点から、生産、出荷までを上田さんが管理している製品があるんですね。
例えば、半導体業界向けのプレス成形品などが代表的ですね。
社内プレス成形~加工~焼成~外注加工(加工寸法指示・調整)~外観検査~寸法検査~梱包~出荷の全工程を管理しています。
――射出成形だけではなくプレス成形のアイテムにも関わっているという事ですか?
はい。射出成形に関しては、現状当社で扱っているCIMアルミナ製品は2アイテムのみです。
射出成形の2品番は前職のノウハウもあり、関わらせていただいているのですが、それ以外にもアルミナのプレス成形の中でいくつかのアイテムの生産管理に関っています。
受注の窓口となっている工場長から受注を伝えられた時点で希望納期を伺い、それに合わせるように逆算して段取りを組み、納期通りに収める事が可能かどうか、可能ではないなら弊社希望納期を返答します。
当社では、今まで、このように厳密に「受注した時点ですぐ納期や生産の日程を確定させる」という事は少なかったのですが、本来ならばお客様の希望通りの納期に製品をお届けする事がベストです。
それが出来るかどうかを検証して、お客様に満足していただくために、計画立案から出荷までを一貫して管理する方法を取るようにしています。
お客様の満足が無ければ事業は先細りしてしまいますからね。
そこは重要なポイントだと認識し、このようなやり方を実践しています。
私はトウゴクセラミックに入ってから初めてセラミックの製造に関わりましたので、そこから色々な人に教えていただいたり、自分でも勉強しながら、何が原因なのか、何が不良の原因となってしまうのか、一つ一つ突き詰めながら改善業務を行っている、という状況ですね。
――素晴らしい試みですね。お話を聞いていると、社長とも直接お話をしているというのも納得出来ます。
いえいえ、わからないなりに、皆さんに聴きながら、といった所です。(笑)
最初は社長にも、こういうお話をしてもいいのかどうかと迷ったのですが、やはり、「不良や不具合を会社の問題点として捉えて、良くする」という目的のもとに、お話をした方が良いと思ったものは提案させていただいています。
もちろん、それをジャッジするのは社長なので、計画を実行するかどうかの判断は社長にお任せしています。
研修の経験から得た一貫した管理体制のアイディア
――社長と言えば、トウゴクセラミックでは近年社長が代替わりしていますが。
はい、元々、私が入社した時に面接していただいたのが、当時専務だった現社長です。
その時は検査課に、定年される方の後継として入る予定で募集され、入社しました。
ですが、その業務をやる上で、「今のままでは効率が悪いのではないか」という疑問が浮かびました。
もちろん、既存の体制があるわけですから、そのまま仕事を進める事も出来たと思います。
ただ、その業務をやる上で「今のままではうまく仕事が回らないんじゃないか」という事を一つ思いました。
そう思ったきっかけは、私が入社直後に社内の全部署を研修として巡った経験です。
当時専務だった現社長からお話があって、一部署2か月ほどをかけて一つ一つ研修として経験させてもらいました。
多分、当社ではそこまで全部署を満遍なく経験させていただいた人は居ないんじゃないですかね。
その時々で「ここの部署ではこういう改善出来る点があるのではないか」という改善点に気付くようになりました。
各部署で問題点を出して改善策を提案し、改善出来るものはその場で改善しました。
――研修で様々な部署を経験した時点で、改善項目が浮かんでいたのですか?
いえ、そこまでではありませんでしたよ(笑)
ただ、色々な部署を見ていく中で「どうなんだろうな」という気になる点はありました。
元々ものづくりをしてきた経験があったので、セラミックとは別業種ではあるものの、「ものづくりをする上で現状のやり方では改善すべき点がある」という事に気付けましたし、それを「どうにかしませんか?」と提案させてもらいました。
――入社時点で前職の製造のノウハウが活かされていたんですね。
そうですね。前職では樹脂が中心でしたが、ものづくりをやってきましたので、「今の会社で私がやってきた事が活かせるのであれば」という事で社長にご相談させていただきました。
それが今の仕事の中でも製品歩留まりの改善と製品不具合のトラブルシューティングの分野になっています。
――製造においては良品を作る事、歩留まりを上げる事は一番重要と言っても過言ではないですからね
会社としては、そこが重要な所だと思います。
不良品が出てしまった場合、そうではない製品と同じ工程は通してしまっているので、その時点で費用が掛かってしまう。その「売り上げにならない費用」をそのまま売り上げにする事が出来れば、大きな利益貢献になると考えています。
歩留まりが悪ければ納期にも影響が出てしまうし、出荷する方も、お客様も困ってしまいますよね。
よって、それを防ぐために歩留まりを上げましょう。歩留まりを上げるために、現状確認をして何が問題なのかを特定して、改善していきましょう。そういう事を一緒にやっていきませんか? という話を皆さんとはさせていただいています。
歩留まりを上げるためのトラブルシューティングという考えは常に持っていますね。
周りからは口うるさいと思われているかも知れませんが、必要な事だと思います。
ロスがどうしても多少出るのは仕方がないとしても、潰せるものがそのまま検査の行程まで流れてくるのはよろしくないと思いますので。
顧客満足度のためのスケジュール管理
――上田さんは他にも焼成工程などにも関わっていると伺ったのですが
はい、焼成工程については、私の前任者が病気で退職してしまった事がきっかけです。
先ほどお話した通り、私は研修で焼成工程も経験していましたが、当時のトウゴクセラミックではジョブローテーションといいますか、他の部署を経験している方はほとんど居なかったんです。
前任者が退職した時に、一部を一緒に作業したパートさんは居ましたが、作業のみではなく、焼成部署の全体を把握している方は、工場長ぐらいしかいなかったと思います。
ただし、工場長には既存の業務があり、研修で2か月ほど居た私が、いくらかは役に立てるのではという事で、そこもやり始めました。
――では、今も焼成工程の管理は上田さんが?
管理の流れとしては、私が工場長に報告し、工場長が最終決定を下す、というものです。
私も一部の作業を実際にしています。
ただ、人手が足らないので、若手の人員を入れていただいて、実際の作業は若手に任せている形になります。
その辺りの管理的なものを担当しています。具体的には日程管理や品質管理ですね。
ただ、品質管理に関しては、先ほどお話した通り、私のセラミックに関しての知見はまだ少ないですので、工場長にも相談しながらになります。工場長は焼成の品質に関するプロですからね。
焼成工程の管理という分野では、納期や生産計画に穴が開かないような日程的なものですとか、焼成前後の製品が品質的にどうかという所も管理しています。
――マネージャーと言うよりはアドバイザーのような立ち位置なんですね。
そうですね。マネージメントもしますし、アドバイスもしますし、と。
ただ、若手に仕事を任せる以上、若手を育てるという事なので、中途入社社員の研修スケジュールの仮組を立案する事なども行っています。
入って来たばかりの若い社員は、社会経験がほとんどない方も居ます。
まず社会的な「仕事をするという事はどういう事か」というものと、具体的に「焼成とはどういう仕事か」というものを両面で教育しながらやっている状況です。
今までこういう社員教育は厳密なスケジュールを立ててはいなかったように思います。
社員教育も、計画を立ててやった方が最終的には近道だと思い、提案させていただきました。
というのも、私は研修で全ての行程を回っていましたので、「各工程で何をやっているのか」という事は基本的には理解していますので。
その経験から、新しい人が入ってきた時に、どこの行程に配属となったらどのスケジュールで教育していくのが一番彼ないし彼女にとって良いのかというのは、案として作れます。
案を作らせていただいて、あくまで一案という形にしています。
最終的には工場長や社長が「ここは足らないからこうしよう」と決定する流れです。私がやっている事は、叩き台を作るようなものですね。
――割合としては製造よりも管理の比重の方が多いのでしょうか?
ものづくりの実務としては、先ほどお話したCIM(射出成形)と焼成工程のみですね。
あとは基本的には管理関係になりますので。QCD(quality, cost, delivery)の管理ですね。
製造は元々インジェクション(射出成形)だけなので、通常の受注量であれば1カ月に5日程度の稼働で生産終了します。
ですから、残りの時間を何かしら管理の仕事に充てています。
あちこちの部署の現場で打ち合わせを行っている事が多いので、基本的には社員やパートさんから私は「どこに居るのかわからない」とか「何やっているのかわからない」とか思われていると思います。(笑)
――では、一日のスケジュールもかなり過密なものになりそうですが
まず焼成に関しては朝一、どこの部署でもそうですが、朝礼を行います。
今日は何をやるのか、その作業のポイントは何なのか、担当者と認識を共有して、OKであればそのまま作業に入ってもらい、何か連絡事項があればその場で注意事項を確認する。
そういう形で、当日から週内くらいの予定を確認します。これは毎朝のミーティングとして10分から20分程度の話ですね。
後は生産管理業務、という事でアイテム別に行程スケジュールを組んであるので、その工程通りに予定が進んでいるかを確認します。
当然、出荷までを管理していますので、製品が上がってきたら検査の実務を担当しているパートさんへの指示もありますし、検査が計画通りに進んでいるかのチェックをします。
寸法測定にも関わっていますので、寸法測定表を作り、それの承認をいただいたら包装・梱包までをやります。その後出荷、と特定アイテムについては全部の行程を管理・実施する事になります。
――という事は、関わっているアイテムについては、最終的にはすべて上田さんの手を通って出荷されていくのでしょうか?
検査の実務自体は私ではなくパートさんや他の担当者にお願いしているのですが、検査結果は私が見て、GOサインを出すかどうかの判断をします。
もっとも、私が最終判断をするわけではないですが、懸念点があれば、上長に打診をして、ジャッジをしてもらう。
そういう判断の要素を抽出して報告する役割ですね。
――やはり、一日のほとんどはデスクに向かっているよりも現場を回っている感じなのですね
デスクに居る時は、基本的には生産計画を組んでいる時ですね。
それ以外の時はもう現場を回って進捗の確認であったり、製品の品質に問題が無いかであったりを見ている、という状態になります。
もう一つ、焼成工程の管理業務として都度の調整が入る事もあります。
焼成で問題が起きた場合や、飛び込みで優先しなければならないものがある場合が、都度の調整として入ります。
そういう大きな流れが、おおよその1日のスケジュールですね。
――お話を聞いていると、かなり多忙なようですが
多忙かどうかという点については、他の社員の方々と大きな差はないと思います。
ただ、現状は特定アイテムに関してのみ工程計画立案後、その進捗管理を行っており、管理方法としてこのようなやり方を他のアイテムでもするかどうか、という事が今後の当社の選択となってくるかな、と私はそう思っています。
顧客満足度と、品質の向上のために
――あなたの仕事は商品が出来上がる上でどのような役割ですか?
これは今までのまとめのようになってしまいますが、3つに分けられると考えます。
1つは、顧客満足度の向上です。
顧客希望に則した生産計画を立案し、順守し、問題が発生した場合はトラブルシューティングを行う。
顧客満足度をどうやって今以上に上げるのか、という取り組みをしています。
2つ目は、品質の確保です。
先ほど言ったトラブルシューティングを含めてですが、品質を確保するためにはどうすればいいのか。
例えば、焼成工程では、製品が良い品質になっているかどうか、焼き上がりの寸法など、色々なものをチェックしている事が挙げられます。
最後に、利益の向上です。
利益を上げるためには、やはり製品の歩留まり改善と、不具合の暫定対策および恒久対策が欠かせません。
その取り組みも行っています。
――特定のアイテムについては、上田さんが居ないと回らないような印象も受けるのですが
計画に関しては、そうです。
ただ、基本的に最後まではプランニングしてあるので、後はその通りに流していくだけです。
……そうでないと私の身体がもちませんからね(笑)
最初の計画立案には確かに時間が掛かりますが、問題点はその時点で解決して、そのスケジュールで行けると決めてしまうので、後はそれ通りに製造が進んでいるかをチェックするだけにしています。
――あなたの仕事は、社会でどんな風に役立っていますか?
代表的なものは、レジャー分野の、釣り具のリールや竿ガイドなどですね。
これはプレス成形のものと、私がインジェクション(CIM成形)でやっている2アイテムの内1つも釣り具に使われています。
後は医療分野の製品や半導体関係でも使われていると聞いています。
そこは、私は営業的な所まではタッチしていないので、細かくは認識していないです。
中々、コンプライアンス上、守秘義務などもありますから、会社としては実務の担当者にはオープンにしていない所もあると思います。
――特に密接に関わっている部署や役職はありますか?
特にどこの部署という事ではなく、全ての部署ですね。
ここまでお話した通り、私の管理業務には全ての行程が絡んでいますし、社長や工場長の判断を仰ぐ事も多いですし、それ以外の品質を確保するだとか、歩留まりを上げるといった改善業務にも全ての部署が関わっています。
「問題が発生していると考えられる所に私が突っ込んでいく」という事になるので、全ての部署との関りがあります。
もちろん、私はあくまで提案する立場ですので、会社の方向性とその提案が違うという事であれば、議論はさせていただき、最終的に調整します。
結果的に、私の提案が会社の方針と対立した事はないのですが。
業務改善、そして若手育成への熱意
――あなたの仕事は社内ではどういう立ち位置ですか? また、周囲からどんな風に思われていると思いますか?
顧客満足度の向上に直接的に貢献出来る立ち位置ですので、重要度としては高いんじゃないかなと思っています。
お客様の満足度を上げる事は、会社の存続であったり、受注を増やす事であったりに繋がると思っていますし、いくらかでも貢献出来ているといいなと思っています。
周囲からの評価としては、正直、良くないと感じています。
正直「あの人は何やっているかわからない」と思われているかも知れませんし、私は既存の方法を改善し、より良い結果、成果に結び付ける事を目的に活動していますが、中でも「変化」は恐いと思われ、敬遠されていると思います。
他部署との連携も積極的に取ろうとしているのですが、どうしても皆さんからは「煙たがられている」というのが実情な気もします。
私はこの会社でお世話になっている以上、「成果を出す事」が一番の重要な項目だと思っています。
成果を出すための改善が必要と感じた場合は、社長、工場長へ問題提起とその改善策を提案し、了承を得て行動するようにしています。
ただ、私のやってきた事が、1年後、2年後にわかっていただけたらいいかな、と考えています。
今は、例え全員の理解が得られないとしても、徐々にこの取り組みに賛同していただいて「一緒にやろうね」となっていければいいかな、と思います。
成果が上がるのであれば、俗に言うwin-winじゃないですか。
会社に取っても良い事ですし、社員にとっても「良かった」と思ってもらえれば一番良いと思います。
――この仕事をしていて、特に苦労したエピソードがあれば教えてください。
そうですね……。
私が現在の管理業務を始めた時、実務を担当する現場の方からは、受注分全ての計画を組まれる事に抵抗感が強かった事が、一番苦労した事ですね。
自分たちで計画を組み、実行していたものに、「計画を組まれる」という事に抵抗感があったんですね。
私は、会社を良くしていく事は、私自身のためでもあり、社員さんのためになると思ってやっているのですが、こういった部分に共感してもらうのは難しく、今後の課題でもあります。
――この仕事をしていて良かったと思う事は何ですか?
1つは、焼成工程の管理方法を1から構築し、計画の見える化を実現、運用出来ている事です。
見える化については、誰でも、そこに来たらわかるように、という事が出来ています。
それを見た若手の社員、新しく中途で入った方からも良い印象をいただいていますから、その部分は有難いと思っています。
2つ目は、焼成工程の若手社員を指導する事により、社会人としての成長を実感出来ている事です。
まだ社会人としての経験が浅い若手に、そのベースを指導する事によって彼らないし彼女らが成長していくのを見られるのは「良かったな」と思いますね。
3つ目は、歩留まりの改善効果を数値化する事が出来、貢献度が明らかになる事です。
データを取っていき、例えば今まで歩留まり7割だったものが何かを改善にして8割になったとします。
こうすると10%の成果として金額換算出来るわけです。
「これだけ利益が出せました」と数値化すれば、改善効果が表せますし、最終的には人事評価に繋げていけばモチベーションに繋がります。
それは一つの柱だと思っていますし、こういう事は必要じゃないかと思います。
――これからの仕事の展望について教えてください
これは中小企業ならばどこもそうだとは思うのですが、ある特定の人に仕事が偏ってしまうという問題があります。
その人がパンク気味になってしまっているのに、他の人は「自分の最低限の仕事だけを終わらせて、終了」という感じだったりするんですね。
これを解決するために、1人の100歩前進よりも全員の1歩前進を目指したいと思います。
社員全体のベースをレベルアップする事が、社員のモチベーションにも繋がるでしょうし、会社としても、それによって大きな方向性の動きが出て来るのかなと思います。
後は、改善する事の貢献度や喜びを共有して、モチベーションに変えていけるような形にしていきたいですね。
何かが良くなったとか、納期が短くなったとか、そういう事を小さい事でもいいので「良かった事」として共有し、それをモチベーションに変えていくのが良いのかなと考えています。
「これは良かったね」「次に活かせそうだね」という風に、前向きになればどんどん良い方向に転がっていくと思うので、そういう風になったらいいな、と思っています。
――職場の雰囲気はどうですか?
中途入社の若手社員が定着しつつあり、社内が今までより良くする思考へ少しずつ変化してきていると感じています。
私個人としては新しく入って来た人とは仲良くしていきたいですし、仕事場以外でも食事に行くなど、コミュニケーションは取っていきたいと思っています。
ベテランの方が身に着けて来た技術を、若手に伝承する事が大切なのだから、若手を潰してしまってはいけない。ベテランは伝える努力を、若手は能力を上げて受け取る努力を、両者が歩み寄るのが大切だと思います。
――ここ数年で仕事の内容に変化があれば教えてください。
そうですね、元々は検査などの一部の業務だけだったのですが、直接お客様とのやりとりをしたりとか、日程の話をしたりとか、より重要度の高い業務に関わる事が増えてきました。
特定のアイテムは生産計画~出荷・売り上げまで担当していますので、それに関連したものは私がやらせてもらっています。
コロナ禍の影響で売り上げの増えた製品にも関わらせてもらっていますし、それが社員のモチベーションに繋がればと思っています。
――普段仕事をしていて、特に感謝している人や部署、制度などはありますか?
関わっている全ての人ですね。
快く協力してくれる方も居れば、苦言を呈される方も居ますが、皆さんに感謝しながら、結果に結びつけるようにがんばっています。
――最後に、このインタビューを見た方へメッセージがあればお願いします。
現在、トウゴクセラミックでは、ベテランの職人たちによる確かな技術力を若手に伝承する取り組みに力を入れています。
今後も変わらず、お客様に確かな品質の製品をお届け出来るよう、鋭意努力してまいりますので、これからのトウゴクセラミックにもご期待下さい。
今回は射出成形課の上田さんにお話を伺いました。
実際にお話を伺ってみると、射出成形の実務だけには留まらず、部署を超えた特定アイテムの工程管理、歩留まり改善や不具合のトラブルシューティング、果ては新人育成スケジュールの立案など、上田さんの精力的な活動には、我々インタビュー担当者も驚かされるものがありました。
しっかりとした目的意識を持った話し方をされる事が印象的でしたが、若手育成に関するお話などからは会社をより良いものにしていこうという、情熱を感じる事が出来ました。
次回は触媒担体・造粒部署の東さんのインタビューを掲載予定です。次回の更新をお楽しみに。