第三回 触媒担体・造粒「職人の技術と感覚」
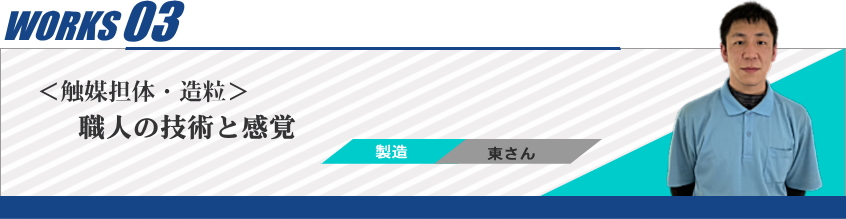
「現場に聴く! 職人インタビュー」では、ホームページだけではお伝えしきれないトウゴクセラミックの製造や生産管理などの情報を、現場へのインタビューを通して皆様にお伝えします。
第三回は、触媒担体・造粒部署の東さんにお話を伺いました。
当社の触媒担体・造粒部署では、アルミナ、シリカ、SiC、コージライト、ジルコニア、ゼオライトなど、様々な素材で粒度分布に優れたセラミック球担体の造粒を行っている事が特色です。
今回はそんな造粒部署から、普段目に入る事のない触媒担体という製品がどのようにして作られるか、それを支える職人の技術と、「現場の声」をお届けします。
「ものを直す仕事」から「ものを作る仕事」へ
――本日はよろしくお願いします。まず、あなたの年齢、役職についてお答えください。
よろしくお願いします。東です。年齢は33歳です。柿野事業所の製造課に所属しています。
僕が担当しているのは製造課の造粒行程。「造粒機での機械のオペレーター」といった方がいいですかね。
入社直後は「ふるい」という、造粒の後ろの工程にあたる作業を2年ほど、下積みという形でやっていました。
造粒の工程は大きく分けると「造粒」という作業と「ふるい」という作業の二つに分かれているんですが、先輩方が作ったものをふるいにかけて、かけて分けたものをまた造粒したり、製品にしたり、という作業がこの「ふるい」にあたります。
先輩から学ぶ形で下積みをしてから、現在の造粒へという作業の担当に移動しています。
――この仕事を始めて何年になりますか? また、以前はどのようなお仕事を?
トウゴクセラミックに入社してからは、8年になります。
以前は自動車の板金工場に勤めていました。
トウゴクセラミックの本社は瀬戸にあるのですが、瀬戸市内で働いている僕の同級生に誘われたことが入社のきっかけです。
僕は元々窯業系の学校を出ていて、その中でもセラミック課というところを卒業したのもあって「セラミックなら多少なりとは、わかるかな」と思って来た感じです。
――となると、全く違う職種への挑戦という形ですね。
そうですね。学校で学んだ事はあるとしても、元々、製造業の経験は僕にはありませんでした。
今までの職種は「ものを直す」という仕事だったので、「ものを作る」仕事もちょっとやってみたいな、と思ったのがきっかけです。
――あなたの仕事について簡単に説明してください。
「原料から球体の粒を作る仕事」って形になりますかね。
セラミック業界向けの言葉で言うと、造粒機で原料……僕らは「種」と呼んでいるんですけど、種に原料を与えて造粒して、製品までのサイズに仕上げるという仕事になりますね。
トウゴクセラミックでは造粒工程をパート分けのような形で作業をしていて、担当パートは大きく「種」と「製品」と呼ばれる工程に分けられます。
「種」側というのが、いわゆる原料とかですかね、「本当に粉の状態」から粒に加工し、その粒をある程度大きくして、特定のサイズ、多くの場合は製品の規格の2歩手前くらいの大きさまで作ります。
それを、今僕が担当している「製品」側にバトンタッチという形で引き継ぎます。
「製品」側では引き継いだ「種」を製品の種類によって決められた、指定のサイズまで大きくしていくという作業になります。
造粒においては仕上げの工程、と言った方がいいかもしれません。
雪だるまのようにセラミックの原料の玉を大きくしていく作業、と言えばイメージしやすいかと思います。
――この仕事を始めた頃に、苦労した事などはありますか?
色々ありますね。
今担当している造粒で言うと、「見てみるのとやってみるのとの違い」ですかね。
簡単に言えば原料というものは「粉」の形から始まるのですが、「粉から球体を作る」という作業が、言葉では簡単ですが、なかなか「理屈とちょっと違う」と言うんですかね、それでだいぶ苦戦はしました。
実際に機械を使って、先に先輩方が作る所を見せてもらって、その後、僕が実際に同じように作るんですけど、全く別のものになってしまってね……。
例えば大きさであったりとか形であったり、ですかね。成形性というか、そういった所で中々上手くいかなくて、どうしたら出来るんだろうとか、そういう形ではいろいろ苦労したというのはありますね。
――良品を作るためには、作業員さんの技術も必要になってくるのですね。
そうですね。どうしても技術職ということで、「手の感覚」をすごく使うので。
造粒は機械の中で「種」、つまり「原料から作った粒」を、泥団子を作る過程のように粉に水をまぶして、粉を与えて、また水をまぶして、と繰り返して徐々に大きくしていくんです。
その工程において、大きくするにも、ただただ大きくするのか、均等に入れた粒の全てに対して、いかに均等に育てるかっていうのは、すごく難しくて、経験がないうちはどうしてもバラバラになってしまう。
同じサイズで入れたはずなのに出来上がると、大きいものになってしまったり、小さいものになってしまったりとか。
この粒度分布に優れた製品を作る事に、日々技術を磨いています。
――あなたの一日のスケジュールを簡単に教えてください。
まず、8時に始業、朝礼と打ち合わせを行います。
僕は班長ですので、リーダーという形で代表して作業員の皆さんにそれぞれ今日の仕事の指示を出します。
本日の作業の目的と、それぞれのそれに対する作業内容が主な内容ですね。
その後、随時そのまま作業を進めていく、と。
その上で、途中途中で確認をしたりして、何かあればそこでまた新しく指示を出したりして、と、そういう形で作業を進めています。
僕は実務の作業を行いながら、品質管理やマネジメントもやっている、とも言えると思います。
そういう事をやりながら、朝礼の後はほぼ一日中、造粒の機械に向かっている、という感じです。
――造粒の工程は、何人くらいでの作業になるのでしょうか?
現状、僕と一緒に作業しているのは4人です。
造粒担当者と、先ほどもお話した「ふるい」の担当者、一対の組み合わせとなって作業を行っていきます。
これを基本単位として「種」側と「造粒」側とで2ペア。
一番ベーシックな人数でやっている体制です。
――造粒担当とふるい担当との連携は重要ですか?
本当にこの2つの作業は二人三脚なので、片方が滞るともう片方も上手く行かないという事になります。
「阿吽の呼吸」ではないですけど、お互いの息が合って来ると、相手が次に何をするかなどを先読みが出来て、下準備がお互いに出来るので、仕事のペースは正直上がりますね。
例えば、新しい方が入って来た時などは、勝手がわからないでしょうし、教えながら、という作業になります。
最初はわからないことが多い仕事になるので、 一緒にちょっとペースを落として、ゆっくりやりながら解説を踏まえてやったりはしますね。
先に言葉だけで説明して、「じゃあ、やりましょう」ってなると、「え?」ってなってしまうので(笑)
実際に動きながら説明し、そこを足しながらやると、まだわかりやすいですね。「習うより慣れろ」ではないんですが。
――具体的には、造粒工程で出来た製品を次々ふるいに渡していく形になるのですか?
そうですね。
造粒で球体を、ある一定の大きさにまでしたら、そちらを機械から出して、出したものをホッパーと言うタンク型の機械に移し替えて、それをまたそのふるいの機械の方に持っていって、ふるいで落として、それを分級する。ふるいは電動の機械なので、自動で震えてそれぞれの大きさに分かれて行くという流れです。
これが造粒工程の基本の作業になります。
原料の球を大きくしていく作業と、網目がいくつもある機械を通して、粒の大きさで振り分ける作業を繰り返す感じです。
ですので、本当に二人三脚というか、「造粒」と「ふるい」の工程は、交互に動いていく仕事なんです。
ふるいが終わらないと造粒の工程に入れないし、造粒が終わらないとふるいにかけるものがない、と。
――では、一日の計画は事前に決まっている形ですか?
そうですね。事前に「いつからいつまでに」といったスケジュールが決まっています。
僕らですと、トン数を基準にしていますね。
1トン作りましょうとか、今月は1日から31日までの基本の月曜日から金曜までで、何日あるので、そこからの日数計算で必要量がここ、今回はここまで作りましょうとか決めますね。
――生産量がトン単位なんですね。
ええ、僕らが作っている製品の出荷量が「1回あたり10トン」とかそういう量になってきますので。
その重量は「焼成後の重さ」です。
実際にはスプレー工程で水分を与えているので、水分やその他のものが焼くことによってなくなります。
なので、焼く前は実際もう少し量があるんですけども、そういうところまで考えながら、「どこまで作ると、目的の量になるか」という計画を立てています。
また、造粒で作っているものは細かい寸法を要求されるものでもあります。
僕らのやっている中で一番多い品種だと0. 5ミリ単位とかになるのですが、簡単に一部分をあと0.5ミリだけ大きくするような事は出来ません。
そこで、計測した粒度の分布を見ながら、例えば原料1キロ分を生産すればいいのか、2キロにした方がいいのかとか、そういったやり方で作業しています。
触媒担体、「目には見えない」商品
――あなたの仕事は商品が出来上がる上でどのような役割ですか?
「ベース」っていう感じです。
形のない原料から、商品となる形、特性を決定付けるようなものを作っています。
これがもう本当にざっくり「工業触媒」としか言えないんですが、「何かの基盤」になるものであって表に出てこないと言うんですかね、正直言うと本当に裏方といいますか、黒子のような仕事になるので。
触媒担体というのは、「これを通して、出て来たもの」が商品となるわけですから、皆様の目には入らないものなんですよね。
僕らが作っているものは、言わば「フィルター」なので、ちょっと表に出ない作業で、お伝え出来る事は少ないんです……。
――あなたの仕事は、社会でどんな風に役立っていますか?
そうですね……。
石油化学や化学工業で使われていますよ、ということだけは伺っているんですが、僕らも「具体的にこういうもの」とは知らされていない事が多いです。
先ほど言った通り「内部で使われている製品」を作る作業なので、表に出せない話が多いみたいです。
僕もトウゴクセラミックに入ったばかりの時は「何かの玉を作ってる会社」というくらいの認識でしたから(笑)
最初は「これをどこかに送ると、世の中の役に立っている」と言われても「?」がいっぱいになりながらも、「セラミックってすごいんだなぁ」って感想でした。
皆さんや僕らも知っているお皿や包丁を作る会社もあれば、当社のように全く表に出ない製品を作る仕事もあるんだ、という風にセラミックの奥の深さを体感したのを覚えています。
社内の連携と、技術の継承
――特に密接に関わっている部署や役職はありますか?
品質管理課や焼成課ですね。
品質管理の方は僕らが作ったものが常に適正であるか見ていただく部署でありますし、焼成前の状態での検査と、焼成後の検査があるので、関りが多いです。
焼成課の方は僕らが作ったものを焼いて、梱包等も含めて出荷までの最後の工程全てを行っている部署ですので、納期の確認などで密接に関わっています。
製造→検査→焼成→検査→出荷というラインで商品を作っているので、どこかが止まると、全員が困ってしまう。
僕らの製造を行っている部署は、そこの最初の要になるので、この2部署とは特に関係が深いと思います。
役職で言えば、製造課の課長さんであったり、焼成課の担当者さんであったり、もちろん、工場長も含めて各部署のリーダーの方とは生産の予定など色々な対応を話し合っています。
――あなたの仕事は社内ではどういう立ち位置ですか?
製造課、シリカ班の班長、という立ち位置ですね。
省略して「シリカ班」と呼んでいますが、正確には「シリカ・アルミナ班」という区分になります。
トウゴクセラミックの造粒部門の製造課では、主に2種類の製品を作っています。
大きく分けて「シリカ・アルミナ」系の製品と「コージライト」系の製品なのですが、この2つは材料が違うため、班分けがされています。
その内の片方の班長を僕が担当している、という形です。
――もう片方のコージライト班とも連携する機会はありますか?
連携は、やはりありますね。
シリカ・アルミナ班、コージライト班ともに、4人のペアで動いていて、そこに課長を加えて9人の体制で生産を行っているのですが、造粒してふるうという、基本の作業は一緒です。
作っている原料の違いや製品の大きさの違いなどはあるのですが、どちらも4人で動いていますし2人1組のペアなので、例えば誰かがお休みになってしまった場合、作業的にペアでないと回らないので代打で向こうへ行って、向こうの仕事を動かすとか、逆の事が起これば僕らの方も助けてもらうとかのような、持ちつ持たれつの関係です。
また極稀にですが、生産の目途が立って、時間の余裕が出来た時等に、時間の取れる限りですけども研修のように互いの班の仕事を経験させてもらう、という試みも行っています。
普段触った事のない他の原料で造粒を行うと、どういう違いがあるのか。
作っているものの形状は、ほぼほぼ同じなのですが、球体の大きさが違うだけで、こんなにも扱いが変わるのか、という部分だとか。
そうすると、技術において新しい発見があったりとか、今後の自分の作業の応用のきっかけになったりだとか、そういう部分が取れれば、と思ってやっています。
――あなたは周囲からどんな風に思われていると思いますか?
周囲から頼られる人でありたいですね。
僕なんかは前職が車関係という事もあって、機械や設備の不具合ですとか、そういった際に呼ばれる事も多いです。
造粒部署の中では、製造課の課長やコージライト班の班長と並んで、僕も作業歴の長い社員となりますので、ベテランと言いますか、中堅と言いますか、後から入社された方に造粒やふるいのアドバイスをしたりする機会が多いです。
そういった部分で今後も貢献していければ、と思います。
造粒を支える、職人の技術
――具体的にはどのような指導を行っているのですか?
例えば、ふるいの工程で言えば、ただ「ふるう」と言っても、原料を流す量を変えたりだとか、振動機の周波数を変えたりだとか、その都度に何が今の作業に適切かとか、そういったことでよく相談とかはあります。
精度と生産性、と言った方がいいんですかね。
処理量が少なくなっても精度が上がる方がいいのか、処理量が早いけれど精度が落ちてしまうのを許容するのか。粒形のコントロールは特に感覚が重要になってくる部分でもあります。
例えば、4.5ミリとか4ミリ~5ミリの製品を作るにあたって、2ミリの球が入ってしまうっていうのは、よろしくないことなんです。ただ、先ほど言った振動とかの流れで、網と網の間で偶然トランポリンのように跳ねて、小さな粒が出て言ってしまう事があります。
そういった時に、振動を抑えたり、ゆっくりにしたりする事によって、球体が網目に落ちやすいシチュエーションを作る。逆に、速くして、一緒に出してしまう設定を採用するか。その判断はその時の都合にもよるんですけど、それがまた本当に大変な所で……。
0. 1ミリずつ、計測結果が粒度分布というので出てくるんですけども、その時に分布を見て、自分たちが狙う場所に対して小さいもの大きいものが、どちらが多いかとか、そうすると先ほど言った振動を強くするべきか弱くするべきか、測定結果を見て、柔軟に対策する必要があります。
――ではふるいの振動数なども、その日によって適切なものが変化するという事ですか?
生産するアイテムによって原則の目安があるため、大まかには変わらないですが、水分を与えて作るものなので、若干ですけど季節の影響があります。
後は、作業者の手の感覚が、真夏と真冬で感覚が違ってしまうという問題もあります。
真冬に洗い物すると冷たい水で手が痛くなるのと同じで、冷たくて感覚が鈍ってしまうとか。
逆に夏場だと気温も高いので、置いておくだけでも水分が多少飛んでしまったりするんですね。
乾いたものをふるうのと、若干しっとりしたものをふるうのとで、周波数を変えるだとか、そういった調整はありますね。
皆さんの思考錯誤した経験を元に、「この時期だったらこれぐらいだろう」というものを全体的に見て、「オールシーズンで見ると基準はここ」というものはあるのですが、実際にやってみた後は微調整が必要になります。
雨の日と晴れた日での湿度の違いもありますし、天候によっても左右されます。
少しずつではありますが、そういった情報を集めて、マニュアル化する試みは行っています。
ここ最近はふるいの方でも新しい方式を始めていますし、それによってまたデータが少しずつ固まってきている所ですから、「新しい機械に対してこういう基準を設けた方がいいんじゃないか」と話し合っている所です。
――では、新人さんの研修などは、そのマニュアルを渡す形に?
マニュアル自体はベーシックな所は作ってあるのでお渡ししますが、新しい方には、特に今言ったような周波数とかは気にせず、「まずやってみましょう」と、一緒に立ち合いながら研修を行います。
先ほど言ったものを見た時に、「触ってもらった水分はどうですか?」という形で、少しずつそこで感覚を得てもらうというか、それの積み重ねですね。
正直、最初の1週間、2週間はもう「わかんないです」っていうのが多いんですけど、 1ヶ月ぐらい経つと、「何となくこういうことですかね……?」みたいになって、半年経つと「今日はこういう感じですよ」とか、「水分がちょっと多いですね」とか「少ない感じはします」とか、わかるようになってくるんですね。
――手の感覚が重要な仕事なんですね。
そうですね。手の感覚は重要な部分になってきます。
もちろん、造粒やふるいをした製品を検査はするのですが、どうしても時間差は発生してしまいます。
その日に覚えてもらった感覚を、検査結果で数字として見た時に、「水分量や粒径がこれくらいですよ」と自分の見たもの、触れたものと数値を合わせるわけです。
なので、新しい方には、「まずは失敗してください」と正直に言ってあります。
失敗する事によって何がいけなかったのか、良くなかったのかを考えてもらえるので、その感覚の精度を上げるきっかけになります。
何となくトントン拍子で上手くいってしまうと、スランプみたいになってしまって「何がいいのかわからない」みたいになってしまうので、逆に失敗してもらって、そこで得た情報の方が次に活かしやすいですね。
思考錯誤が必要な部分は、ものづくりとしての面白い所でもあり、難しい所だと思っています。
新しく入った方の中でも、今言った「作ること」が入ってから楽しくなる人も居ますし、「さっきまで粉だったものが粒に出来るのが楽しい」って言って、それでやってみたいとやる気を出してくれる人も居ますし、「やってみたら面白かった」という人は多いですね。
五感全てを使う、職人の感覚
――お話を聞いていると、職人が職人を育てる職場、とも言えそうですね。
どうしても、「感覚」の習得は不可欠になってしまうと思います。
先ほど言った、「ふるい」の工程をやっている方でも、ある時に研修として「ちょっと作ってみますか」と造粒の工程を体験してもらうと、「普段、横で見ていただけだけど、こんなことやってるんだ」みたいな感想をもらう事があります。
例えば、僕が造粒の作業しているのを見ていると、何となく「大きくなったな」とか、「粉から粒になってるな」という程度で、「どうやってるんだろう」くらいの認識なのですが、実際にやってみると、「これは、全然理屈じゃないですね」と納得してもらえる事が多いです。
「何か楽しそうにやってると思ってたけど、それどころじゃないですね」なんて言われたりしました(笑)
――技術的に、どうしても体験してみないとわからない部分もあるんですね。
自転車で例えたらいいんですかね……?
自転車も最初、いきなり乗っても乗れないじゃないですか?
最初は補助輪を付けたり、経験者が一緒に付いて後ろを支えてもらったり、何度も倒れたりするんですけど、その失敗をしながら、何かの「コツ」を掴んだ瞬間に乗れるようになる、っていう。
ちょっと長い目は必要になるんですが、その「コツ」がわかると、「あー、こういう事か」と技術を習得していく。
自転車でも、プロの方はそれにどんどん技術を積み重ねて技を極めていく、と失敗し続けた先にはそういう段階があると思っています。
造粒に使われる技術は、インターネットとかで調べても出て来ないような事なので……。
かと言って、これを簡単に文字や絵で見せたとしても、正直、理解が難しいかなっていうのもあります。
よく授業でやるようなビデオ研修や教科書での研修も、「見る」事は出来るんですけど、「実際それを自分がやる」となると、訳が違うというような事になると思います。
幸い、僕は前職が板金関係でしたので、凹んだものを直したりする時の「手の感覚」というものには慣れていました。
そのような感覚の応用が出来たので、僕はこの仕事が向いているのかなあ、と思っています。
――人間の目と、手の感覚に頼っている部分も大きい、と。
そうですね。
僕らで言えば「目」と「手」の感覚……あとは「耳」もそうですね。
機械の中で原料が転がる時の音っていうのも判断の基準にしています。
――音、というと、原料が流れる「サーッ」というような?
そうですね。
その「サーッ」という音が、水分が少ないと、いわゆる甲高い音になって「シャーッ」という感じになりますし、水分を与えると静かな音になります。また原料を与えたりして荒いものが混ざると、独特の「ザラザラ」とした音が混ざってきますし、その音の違いを、水分の量はどうか、転がり方が上手く行っているのかどうか、と判断する材料の一つにしています。
目と手と耳、五感を使う仕事なので、格好良く言えば、芸術品を作るのにも近い感覚の職人仕事になってしまいますね。
――先ほど、「まずは失敗してください」と教えていると仰っていましたが、そうした場合の失敗した原料はどうなってしまうのでしょうか?
トウゴクセラミックでは、失敗した原料は、もう一度乾燥させて、粉砕してから粉に変え、いわゆる「再生原料」として転用しています。
なので、先ほど言ったように、新しい方には、まずは体験して、失敗してもらう方針を取っていますね。
新しい方がまずやってみた時、水加減とかもわからないですから、正直ダメなものが出来てしまう時もあります。
でも、それをやった事によって、普段僕らが作っているものが、どういう状態で出来ているか、というのがわかってもらえるきっかけになります。
大げさに言うと、研修の間に「やったらダメ」って事をやってもらった方が、どこまでが良くて、どこからが悪いのかの基準が身に付きますからね。
例えば、水を与えすぎたら整形が崩れてもう完全にいわゆる泥になってしまうので、「ここまでやったら泥になってしまうんだよ」とか、逆に、「ここまで原料を与えすぎると見た事も無いような丸くない形のものになってしまうんだよ」とか、実演を兼ねて学んでもらっています。
原料が再利用出来ずに、「これは破棄だからね」と言われてしまうと、新しい方もハードルが上がってしまうので、この仕組みには助けられていますね。
逆に、実生産ではコンセプトとして「限られた原料で作る」という事は意識しています。
目標として、「この10トンの原料で最終的に12トンの製品を作りましょう」とか、今月の生産予定を決めたりするんですけど、そういったシミュレーションを日々やる事によって、無駄を減らしていく方針です。
実生産の時に、先ほど言ったような失敗を減らせば、無駄はもちろん減りますし、後は品質管理をしながら、いかに無駄を省けるかを心がけています。
かつ、「良いものを作る」という事を目標として、それぞれが日々、ふるいも造粒も、種側、製品側に限らずお互い「何をしたら良くなるか」と話し合っています。
新しく入って来た方など、まだ経験が浅い方も居るので、そこを経験者が一緒に引っ張りながら、という形ですね。
職人の技術の伝承という課題
――この仕事をしていて、特に苦労したエピソードがあれば教えてください。
やはり、先ほどの話の通り、造粒の難しさが一番でした。
感覚論なので、「コツ」もそうですし、後は「機械の特性」と、その両方を理解できるまでに苦労しました。
使っている機械も、全て同型機ではないものですから。
新しい古いの年式であったりとか、微妙にメーカーさんが違ったりだとか。
そういった所での、「この機械にはあるけどこちらにはないもの」、逆に「こちらにはあって、向こうにはないもの」とか、機械の特性として、向いている製品と、向いていない製品とがあったりするんですね。
もしくは、それを両方の機械でもできるように、「自分がそこの手助けをするという」技術を習得するだとか。
先ほどの話の中でも「粉から粒を作る」という最初の工程が、すごく難しいところで、そこは本当に苦労しました。
格好良く言えば、「無から有を作る」段階になるので。
――やはり新人さんにそういった事を教えるのにも苦労しますか?
そうですね。
もう最初は、何度も実演というか、「見せる」事から始めます。
例えば、一緒に僕が立ち会って、まず作って見せて、その次は解説を交えて作ります。
その次はそちらの新しい方にまずやってもらうんですが、細かい指示を出しながら一緒に作ります。
で、その次は横には付きますが、特に指示は出さずに、まず同じ事をもう一度再現してみましょうと。
作った時に、同じものが出来れば問題はないんですけども、違うものが出来た時には、「何が違ったと思いますか」と。
例えば、造粒工程では、スプレーで水を与えるんですけども、それを止めるのが遅かったとか、必要量以上に水を打ってしまったために別のものになってしまったとか、もしくは、水を少なくしてしまったために別のものになったとか。
後は、「手の動き」というんですかね。造粒やふるいには、手を入れながらやる作業もありますから。
――習得する技術には、「手の動き」まであるんですね。
そうですね、量が少ない多いと言うか、ちょっと細かい所の感覚を掴むために。
基本は手を入れない作業が多いんですけども、感覚を掴むまでの所では、あえて知って欲しいのもあるので、手を入れてもらったりとか、もしくは作った球体を、機械止めてから触ってもらったりとかして。
見てもらって、体験してもらって、本当に「育てる」っていう言葉で言うと、1粒1粒を、いかに均等に原料を与えていくかみたいな所に通じるものがあると思います。
――ですが、「感覚」と言うものは人それぞれ違う事もあると思いますが?
そうなんですよ。
先ほど言った、「一緒に並んでやる」というのは、「その人じゃないとわからない感覚」があるからなんですね。
わかりやすく水分の違いという話をしたのですが、僕がやったものを見せて、全く同じ事をしてもらったのに、違うものが出来る事もあるんですよ。
水や原料も決められた量でやったにも関わらず、です。
そういう時は、手の動きの違いが関わっている事が多いです。
手で原料を均(なら)したりするのですが、その際に原料を無意識に握ってしまったせいで塊になってしまっていた、という事もあります。
後は、手の大きい方も居れば小さい方もいらっしゃるので、そこでもやり方が変わってきます。
僕の場合は指3つ分の面積で原料を広げると上手く行くものが、人によっては4つ分だったり、その間だったり。
最近は水分量もデジタルですし、原料の投入量も数字化されてきたので、「決められた指定数を打ちましょう」というマニュアルも整ってきたのですが、僕が入社した直後の時代は、全部感覚でやっている「本当に職人仕事」だったので、非常に苦労しました。
――現状で運用しているマニュアルを作るのにも苦労されたんですね。
そうですね。
最初はもう何もかもが「感覚」だったんですよ。
原料を握った時の水分だとか、音だとか、と言われても、最初はちんぷんかんぷんですよね?
先ほど言ったように、ダメな事をした時に、初めて「こんな音出るんだ」とか、「水を与えすぎると機械にこんな不具合が出るんだ」、とか。
今は、工場長の方針もあり、そういう事をみんながわかるように、まず原料と水の関係を数字にして、それを元にマニュアル化が進んでいます。
そこに、後は補正が加わるのですけど、そこだけがまだ、その都度の気候や環境で変わる、という現状です。
例えば、先ほど言ったように、種も毎日作っているものですから、土日を挟んでいると水分が減ってしまう。そうすると、「最初に与える水の量を、今日は普段よりこれくらい増やしましょう」とか、そういった調整をしています。
基準があって、都度の調整が入り、より作業員が解釈しやすいようにと変わっていますね。
――改善はされていても、まだまだ職人仕事の部分がある、と。
ええ。
補正とかの基準っていうのが、中々設けにくくて……。
気温、湿度、天候だとか、そういうものは統計で取っても中々……実際、1年前の今日とそれらの条件が同じかって言われたら、やっぱり違うものになってしまうので。
その辺りをまず、水分と原料の量が一緒になれば、「余程の事がない限りは基準の中に入るだろう」というマニュアルを工場長にも考えていただいて、という運用をしています。
テストで言えば、「80点以上が合格」というような形を設けて、その中で、職人の皆さんに「自分自身の感覚」を身に付けてもらって、調整してもらう。
流派と言いますか、それぞれの感覚は違っても、求める答えは同じ所に持っていけるように、という考え方です。
検査結果っていうのは絶対なので、数字を出すために、ある人の感覚だとこういう事をすると、この基準に入る。僕の場合はこういう事をするとこうなんですよ、と。
多少の違いはあれど、お客様に収める製品の寸法は同じです。良品を作れるようにという目標は一致しています。
そういう意味では、朝礼や現場の後半などでノウハウや気付いた事を共有する事はとても重要ですね。
4人1班でフォローし合うように動いているので、縦や横、時には斜めの繋がりにも、助けられています。
たった1粒を作るまでの長い道のり
――この仕事をしていて良かったと思う事は何ですか?
良かったと思う事は、まずは、自分の好きな仕事が出来ている、という事ですね。
「たった1粒を作る事の難しさ」は、苦労した事でもあり、経験出来て良かった事でもあります。
製造業の中でも、中々接する事がない業種に携われた事と、先ほど言ったように「たった1粒を作るまでの長い道のり」を知る事が出来たのは、得難い経験だと思います。
単純に「転がして終わり」じゃないんだな、と。
セラミックと言っても「触媒担体」というジャンルは余り知られていないですし、コージライトやシリカ、アルミナでそれぞれ触媒担体としての新しい役割がある事だとか、窯業系の学校で学んだ知識よりも深い所を知る事が出来ました。
――これからの仕事の展望について教えてください。
今以上に、より「造粒」という技術を身に付けたいですね。
僕自身も、まだまだ技術としては未熟だと思っていますし、畳職人や大工さんのような、いわゆる「職人の仕事」ではないですが、死ぬまで勉強だと思っています。
今は既存品の生産がメインなので、前任の方たちが引き継いできた情報があるんですけど、量産のみではなく、試作品にもチャレンジしていきたいです。
例えば、当社では今まで取り扱った事のないような材料だとか性質だとか、特別な「今まで触った事もないようなもの」を造粒する事になった時、自分たちが得たもの、積み上げて来たもので出来るのか、という挑戦をしてみたいという探求心もあります。
そういう新製品を作る機会が来た時の為に、自分の技術を磨いていきたいと思います。
既存の製品の品質向上についても、コストや再生率の面で、自分たちが貢献出来れば、と思っています。
――職場の雰囲気はどうですか?
職場の雰囲気と言うと、4人チームで動きながらそれぞれのパートに対して意見を言ったり、改善点を出したり、そういう事を話しながら作業しているのですが、まず機械が常時動いているので、距離は近くなってしまいますね(笑)
新しい方が見えると5人での作業になったり、時々他部署への応援があったりはしますが、いわゆるアットホームというか、良い雰囲気だとは思います。
当社では近年、世代交代の兆しもあり、僕もそうなのですが、若い世代の社員が増えています。
若い方からベテランの方まで、また外国出身の方もいらっしゃいますし、老若男女、明るくコミュニケーションを取りながら仕事をしています。
――ここ数年で仕事の内容に変化があれば教えてください。
現在の部署での、班長になった事ですね。
今までは製造課の課長が僕のポジションで生産を行っていたのですが、この数年で僕も経験を積みましたし、独り立ちというような形で引き継ぎました。
生産計画のベースを作ったり、1日の作業内容を決めたり、それを一緒に作業するグループの方へ指示を出していく、というような、今まではそういう指示は「もらう側」だったんですが、指揮者の方になった事は大きかったですね。
指示を出す側になると、先ほどお話したように、「感覚」の話を避けて通れなくなるので、そこには苦労しました。
言葉だけで説明しても齟齬が生まれてしまうので、少しずつコミュニケーションを取りながら、「こうすると良くなるよ」とか「こうすると自分の作業も楽になるし、後の工程の人も助かるよ」とか、「品質改善のためにはこんなやり方もあるよ」とか、手法を紹介して、後は自分なりの感覚でアレンジしてもらう、という流れです。
ただ、自分なりの手法を見付けてもらっても、最終的に出来る製品は、みんな一緒のものになるように、前提の共有はしているつもりです。
――普段仕事をしていて、特に感謝している人や部署、制度などはありますか?
まずは、柿野工場の工場長ですね。
今のシステムに対して、あの手この手と様々な改善でご助力をいただきました。
そして、僕自身の師匠と言いますか、今の製造課の課長さんですね。
課長からは「造粒とは何か」という所から今の自分の技術になるまでを教わりました。
後は、やっぱり、自分が生産で大変だった時に、他部署から応援に来ていただいたり、困った時に助けてもらったりした、社員の皆さんには、本当に感謝しています。
――最後に、このインタビューを見た方へメッセージがあればお願いします。
造粒という手法を考えた時、ご依頼頂ける業種は限られていると思います。
この機会に、トウゴクセラミックの技術を、商品と共に見ていただき、その中で弊社がお役に立てるものが見付かればと思います。
転動造粒ならではの、強度面にも粒度分布にも強い球体をお探しなら、是非、トウゴクセラミックにお問い合わせ下さい。
また、ここからは採用希望の方へのメッセージとなってしまうのですが、
正直、「触媒担体・造粒」という業種は、一言では表現出来ない、複雑なものです。
それでも、見て、触って、体験してもらう事で、あなたが何かを得られれば、それは素晴らしい事だと思っています。
よくある言い方かも知れませんが、「ものづくり」が好きな方には「何かを作る」という楽しみが得られる職場だと思います。
興味のある方は、是非、当社の求人にご応募ください。
今回は造粒製造課の東さんにお話を伺いました。
実際にお話を伺ってみると、「造粒」という、セラミックの中でも特殊な製品を作る上では、こんなにもたくさんの職人の技術や経験が活かされているのだと、新たな発見がありました。
中でも、東さんの話す、「作業者それぞれに流派はあれど、最終的にお客様へお渡しする製品は同じものを」、「死ぬまで技術を磨いていきたい」という言葉からは、トウゴクセラミックの触媒担体・造粒製品を支えているプロフェッショナルたちの向上心と、熱意が伝わってきました。
次回は焼成部署の沼田さんのインタビューを掲載予定です。次回の更新をお楽しみに。