第五回 検査・出荷「多品種検査の裏方」
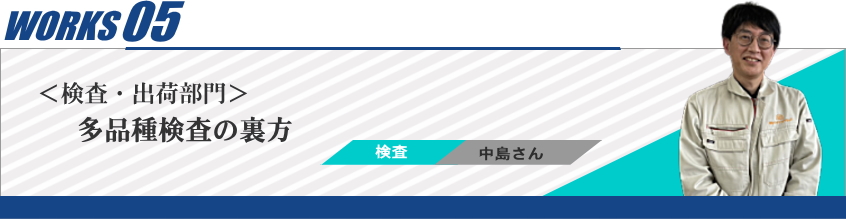
「現場に聴く! 職人インタビュー」では、ホームページだけではお伝えしきれないトウゴクセラミックの製造や生産管理などの情報を、現場へのインタビューを通して皆様にお伝えします。
第五回は、検査出荷部署の中島さんにお話を伺いました。
当社の扱う製品群は、電子部品、触媒担体、医療部品、エンジニアリングセラミックス(半導体部品などの各種絶縁体部品、耐摩耗部品、耐熱部品、耐食性部品)等に多くの実績があり、実に多品種なものとなっています。
今回はそんな2000を超えるアイテム数の商品をお客様の手元に届ける最後の工程、検査出荷部署から、多品種、精密部品を扱うからこその苦労や意気込みなど、「現場の声」をお届けします。
多品種を支える検査業務
――本日はよろしくお願いします。まず、あなたの年齢、役職についてお答えください。
中島です。52歳。ポジションとしては、検査の検査、出荷の部署になります。
今は入って間もないので、上司の方に教えていただきながら、仕事を覚えて居る最中ですね。
――この仕事を始めて何年になりますか?
研修の後、今の検査部署に入ったのが4月の事ですから、もうそろそろ1年になります。
――こちらの仕事に就くまでどんな仕事されていましたか?
電子部品関係の、研磨の仕事に就いていました。
製品の表面を磨く仕事ですね。
――では、全く違う業種からの転職という形に?
はい。
トウゴクセラミックにも加工として研磨の工程はあるのですが、全然色味が違うというか……精度も違いますし、やっている事は違う印象ですね。
――業種が変わって、戸惑った事や困った事はありましたか?
やっぱり、「品種が多い」事ですかね。
当社は様々な製品を扱っている事も特色なのですが、何しろ物の種類が多いのでそれを覚えるのが大変ですね。
今の所、まだ私も全てを把握しているわけではないですから。
新しい製品も日々増えていますし、既存の製品も沢山あります。
入って間もない私はその両方を覚えていかなければいけないので、そこがちょっと大変かな、と思っています。
――新しい製品を覚えていく上で、工夫している事などはありますか?
そうですね。まあ、やはり、ノートは小まめに取っていますね。今の所ノートぐらいしか、自分の記憶を履歴として残していく事が出来ないので。
――そうなると、ノートも膨大な量になりそうですが。
今だと……5冊目ぐらいですかね。(笑)
もう品種が、前の会社に比べても、各段に多いので。
製品によって、基本的なルールは同じでも、ちょっとずつ微妙にルールが違う事があるので、そういう所はやっぱりノートを確認しないと難しいですね。
「ここの会社さんはこういう風に納品するんだけど、品種が違うと少しルールが違うよ」みたいな所がありますし、そこは、ノートを見ながら確認して、一つずつ間違いが無いようにやっています。
公差1000分の5mm、ミクロン単位の精密検査
――あなたの仕事について簡単に説明してください。
基本的には「製品の検査と出荷」なんですけど、精密な測定機器を使用して、ミクロン単位、つまり1000分の1mmの単位まで測定を行います。
画像測定器だとか、そういったもので細かい所までお客様のご要望に応えて検査票を作成する、という仕事ですね。
お客様が求める寸法に対して、当社の製品が要求に応えられているのかをチェックする仕事と言っても良いと思います。
もちろん、測定機器だけではなく、目視検査も行います。
傷や欠け、汚れ等をチェックするのですが、その許容範囲が製品によって違うのが大変ですね。
例えば、一言に「傷」と言っても、傷が長くても薄ければ良品として扱う製品や、傷が短くても深ければ不良として扱う製品など、基準がそれぞれにあります。
そういった非常に多岐に渡る検査項目を、検査をされているベテランの方に教えてもらいながら、少しずつ覚えている最中です。
――特に検査をする上で苦労した製品などはありますか?
やはり、難しいのは、マイクロメーターや画像測定器で測る必要がある、公差が少ないような製品ですね。
例えば公差が0.1mm程度であればまだノギスの範囲なので良いのですが、それが、公差1000分の5mmとかになってくると、商品としては取り扱いが難しくなりますね。
規格に入るまで持って行くのも大変ですし、どうしても不良が出たりします。
より厳しい検査が求められる反面、世の中の流れとして、製造業でもそういった細かい規格の精密部品が必要とされているのかもしれないと感じています。
全ては、「お客様のもとへ商品を届ける」ために
――先ほど「製品の検査と出荷」と伺いましたが、出荷の方ではどのようなお仕事を?
出荷は主に梱包作業ですね。
運んでいる最中に製品が壊れないように、製品に保護材を巻いたり、保護資材に詰めたりして発送する業務です。
傷付いたり、破損したりとか、そういう事がないように送り出すという仕事になってきます。
――出荷の業務で特に苦労する事などはありますか?
そうですね……。
例えば、たくさん送る時とか、一箱が重くなったりするんですね。
そういうものをダンボールで送ったりすると、底が抜けないように気を付けなきゃいけなくなります。
そういう所も間違えないように、自分である程度の重さを把握して、最初から補強材を入れておいたり、そういう事には気を付けています。
あとは、宛先ですね。
流石に宛先を間違える事は、そうそうないのですが、「納入先さんと、注文先さんが違う」というケースもあるので、そういう場合は、特に間違いが無いように気を付けています。
それに伴う納品書の扱いだとか、事務的な部分でもミスが無いように注意しています。
――あなたの一日のスケジュールを簡単に教えてください。
運送屋さんの引き取りが午後からあるので、基本的に午前中は出荷の作業を行っています。
引き取りが多い日もあれば少ない日もあるのですが、出来るだけ午前中に当日分の出荷準備を終わらせます。
その後、次の日の分の出荷の準備を始めます。
「午前中に出荷作業が終わるように、前日までに準備しておく」というスケジュール感ですね。
その際に、必要な検査表等のお客様が要望する資料があれば、それらも用意します。
測定や検査の業務はここに含まれます。
このように「前日までに翌日の出荷が出来る状態にしておく」という作業がほぼ一日の流れになります。
お客様に送るものに対して、足りない資料を当日の午前中の内に用意するとなるとバタバタしてしまいますので、一緒に送る資料がある場合は、前の日までにしっかりと準備しています。
我々はお客様のもとへ商品をお届けする最終工程ですので、出荷する当日は、本当に梱包するだけという形にしておかないといけません。
――となると、出荷のスケジュールがとても重要になってきますね。
そうですね。
出荷が多い日もあれば、少ない日もあるので、出荷が多い日のために、前もって出来るものだけ優先的に準備しておく等、考えながらやっています。
在庫管理や必要部材の調達も、その出荷をする為の事前準備として行っています。
何しろ、当社は製品の種類が多いものですから、在庫数のチェック、検査表の作成、梱包材の準備、細かい所では検査に使う手袋や、ボールペン等の備品の在庫確認、補充等、準備にかける時間は多いですね。
後は、私もまだ覚えている最中なのですが、外注加工の段取りも行っています。
全ての製品が当社で一貫生産しているわけではないので、製品によっては、製造過程で外注加工を依頼する場合もあるんですね。
業者さんに外注加工を依頼するためには、そのための発送、引き取りなどの作業が発生するので、それにもまた、必要なものを準備して、期日までに送って、加工されて返って来た製品を検査して、という業務になります。
これらも全て、「納期までにお客様のもとに商品を届ける」という最終的な出荷作業のためにある仕事と言っていいと思います。
とは言え、私はまだ1年目で経験が浅いですので、スケジュールの管理や他部署との連携は、まだベテランの方に助けて貰いながら、という状況ではあります。
毎朝の朝礼で、当日のスケジュールを予定表で共有するのですが、その前に、私の作った予定表を、上長の方に見ていただいて、最終確認をしてもらってから、発表するという形です。
不具合品を流出させない、最後の砦
――あなたの仕事は商品が出来上がる上でどのような役割ですか?
やはり、検査出荷部署の役割は、お客様に不具合品を流出する事なく出荷していく事だと思います。
そのために、さっき言ったような検査表を作ったり、目視検査したりしているわけですから、当たり前の事かもしれませんが、不具合品を決して流さない事には注意しています。
――あなたの仕事は、社会でどんな風に役立っていますか?
聞いている所によると、レジャー用の釣具や、電子部品関係で使われているとは伺っています。
――特に密接に関わっている部署や役職はありますか?
前工程のバレル加工とは密接に関係していますね。
そこでの仕上がりが、検査の歩留まりに直結していますので。
――では、特に仕事で使っている、重要な設備などはありますか?
やっぱり、測定機器は重要だと思います。
三次元測定機や画像測定器、あとやっぱりノギスとかバイトとかは使用する機会が多いですね。
寸法を測る機器に触れる事が多いです。
あとは、面粗度測定器でRa(算術平均粗さ)を測ったり、光学顕微鏡で表面の傷や汚れを確認したりする工程もありますが、私はそこまで多くはないですね。
――あなたの仕事は社内ではどういう立ち位置ですか?
お客様に不具合品や規格外品を出荷しないようにするための、最後の砦、といった感じでしょうか。
役割としては、やっぱり、期日までに納品する事、不具合品を出さない事の2つですね。
不具合が出れば、当然、お客様の検査に対する要求が上がってしまいます。
例えば、現状が「5つの抜き取り検査でいいよ」となっている製品が、抜き取り検査30個になってしまったり、下手をすれば全数検査になってしまえば、その分、労力が掛かってしまいます。
そういう意味で、製品の品質を守る事は、コストを守っていく事にも繋がっていくと思っています。
仕事を覚えるための、強いモチベーション
――あなたは、周囲からどんな風に思われていると思いますか? また、どう思われたいですか?
入社間もないので、周りからどう思われているかは、正直わからないというのが現状です。
今後は、業務を覚え、周りから信頼を得たいと思っています。
今はまだ、自分の事で精一杯なので、仕事を覚える事に専念して、という所ですね。
やっぱり、当社の製品は、ものすごい品種があって、それを把握して行くには、「どうしようかな」って思っているくらいなので(笑)
もちろん、普段から定期的に出荷される製品については問題ないのですが、2か月に1回だとか、3か月に1回だとか、そういった少数でありながらも多品種な製品をどう把握していくかが、今後の課題だと思っています。
――この仕事をしていて、特に苦労したエピソードがあれば教えてください。
まあ、常に苦労していますね(笑)
当社は製品の品種が多く、同じような製品でも、少し大きさが違うだけでも別の扱いになっていたり、覚える事に今も苦労しています。
例えば、小指の先ほどの小さなリング状の製品でも、1mmや2mmも径が違えば材質が同じでも、全く別の商品になってしまいます。
そうなると、「この形だったけど、こっちがこの名前で、あっちがあの名前で、えーっと……?」となってしまったり(笑)
また、商品の名前も、名前の語尾が違ったり、同じ商品でも名前が違ったりとか、各商品の規格番号も当然あるのですけど、社内でその回っている名前、商品の規格の001とか002っていう番号で呼ぶ人もいれば、その商品名で言われる方もいますし、お客さんの方もその製造番号で注文してくるっていうよりも、名前のほうで注文してくるお客さんもいらっしゃるし……。
そういったものをリンクして覚えてかなきゃいけないので、ノートが欠かせないですね。
――この仕事をしていて良かったと思う事は何ですか?
そうですね……。
今もそうですけど、入社当時は本当にかなりテンパっていて、良かったと思う余裕が無かった、というのが正直な所です。
けど、私もだんだん年を取ってきて、「人の優しさが身にしみるなぁ」と思う事は増えましたね。
どんな事にしても、ちょっと迷っている時にとかに、手を差し伸べてくれたりすると、やっぱり「ああ、助かるなぁ」と思いますね。
現状ではまだ、「していただいていることに対して、まだお返しが出来てないな」という気持ちがあるので、自分がある程度、細かい部分までわかってきたら、今度は逆に困っている人たちに手を差し伸べたいと思っています。
――これからの仕事の展望について教えてください
もう少し、システマティックに仕事が出来るようになればと思います。
例えば、手順書や標準書など、基本となるものを、今より整備していければと思います。
何れにせよ、会社の方針に合わせてやれる事をやっていく形になると思いますので、まずは、業務を覚えて、効率良く検査出荷業務を循環させられたらと思います。
――職場の雰囲気はどうですか?
検査部署は、皆さん一生懸命やっているので、そんなに仕事中に会話があるわけではないです。
「不良品を出さないように」と検査している時に、話しかけるわけにはいかないですから、雰囲気としては黙々と作業しています(笑)
休憩中にちょっとしたお話をするくらいかな、と思います。
――ここ数年で仕事の内容に変化があれば教えてください。
特別な事は言えませんが、この仕事を始めてから、毎日が早いというか、「一生懸命やっている実感」をすごく感じています。
「今までの人生の中でも、結構頑張ってるぞ」という充実感はあります。
――お話を聞いていると、中島さんからは、多岐に渡る品種を検査する業務にチャレンジする、強いモチベーションを感じます。精力的に仕事をする上で、自分を支えているものはありますか?
基本的には、「色々な事を知りたい」という欲求があるんですよね。
広く浅くでもいいので、何でも知っておきたい。何かあった時の選択肢を、知識として自分の中に持っておきたい、という気持ちは常にあります。
これは、昔、一緒に仕事をしていた方に、とても知識があって仕事の出来る方が居て、「この人みたいになりたい」と思った影響もあると思います。
そういう部分が、多品種に渡る業務を覚えるモチベーションになっているかな、と思います。
――普段仕事をしていて、特に感謝している人や部署、制度などはありますか?
働いている同じ部署の人には感謝していますね。
やっぱり、教えてもらったりとかしていますから。
そういう人たちがいなければ当然、一人で仕事はできないですし、何とか頑張って、早くこの人たちのために仕事を覚えていきたいなと思っています。
――最後に、このインタビューを見た方へメッセージがあればお願いします。
ファインセラミックスという分野は、まだまだこれから発展していく余地があると思います。
例えば、窒化ケイ素などは軽くて耐久性が高いという特性を活かして新たな要素に使われていく可能性がありますし、現状でも電子機器だけではなく、釣りの道具などにも使われています。
他分野へと広がっていくセラミックと関わっていく事で、私自身も、視野を広げていければと考えています。
新素材としてファインセラミックをご検討の方は、ぜひ一度、トウゴクセラミックにお問合せ下さい。
今回は検査出荷部署の中島さんにお話を伺いました。
実際にお話を伺ってみると、製造の現場だけではなく、検査や出荷の現場でも、職人さんたちの頑張りがトウゴクセラミックの2000を超える製品が出来上がってお客様のもとへ届くまでの道を支えているのだと、新たな発見がありました。
中島さんの真面目な姿勢と、検査出荷業務のノウハウを少しでも早く習得しようとする強いモチベーションは、精密かつ多品種な製品を扱う当社の検査部署ならではの苦悩と共に、インタビュアーの印象に残っています。
次回は経理総務部署の宮地さんのインタビューを掲載予定です。次回の更新をお楽しみに。